Knowledge and experience that results in agile performance and excellent quality
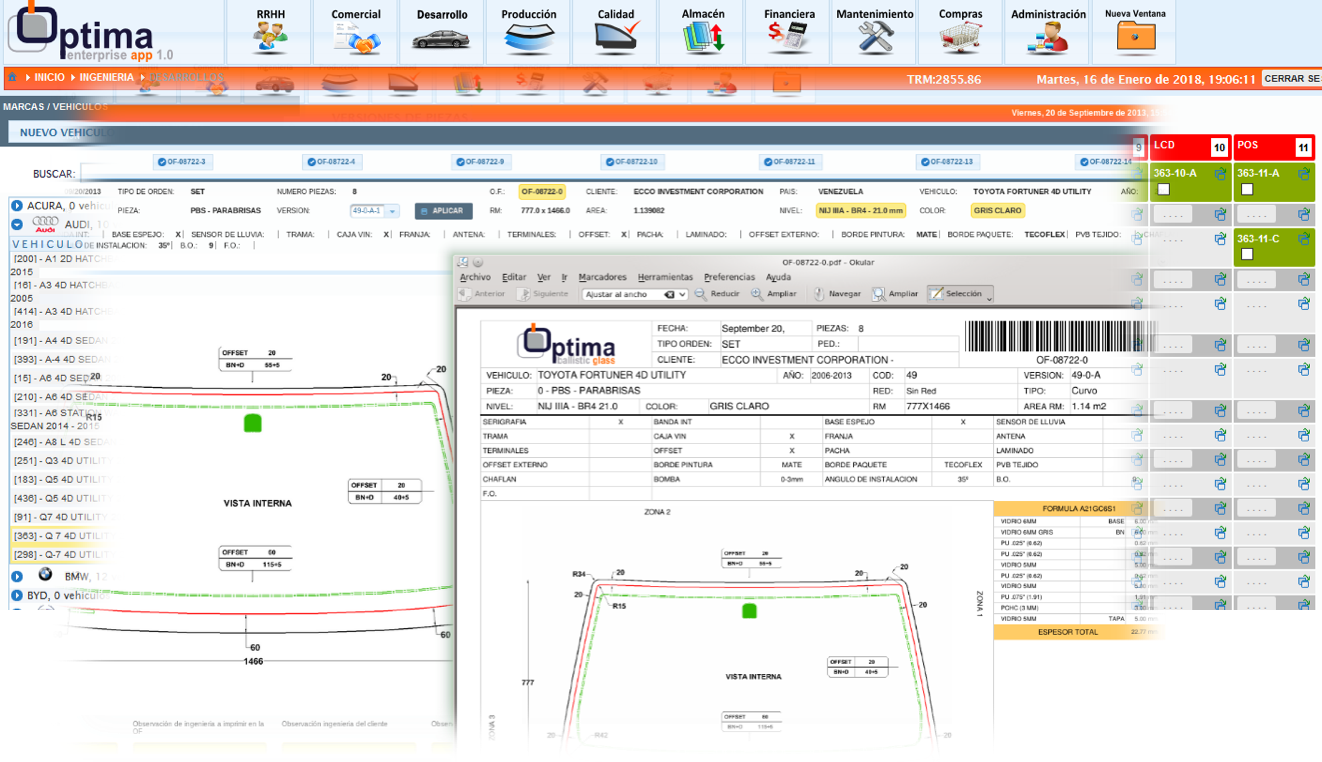
Exceptional technical communication
• Digital control of design by model and client version
• In-house development process, industry's quickest service
• Centrals for the precision of curves in the product
• Real time digital production control.
• Database with more than 600 vehicle designs
• CNC 2D and 3D cutting and polishing processes.
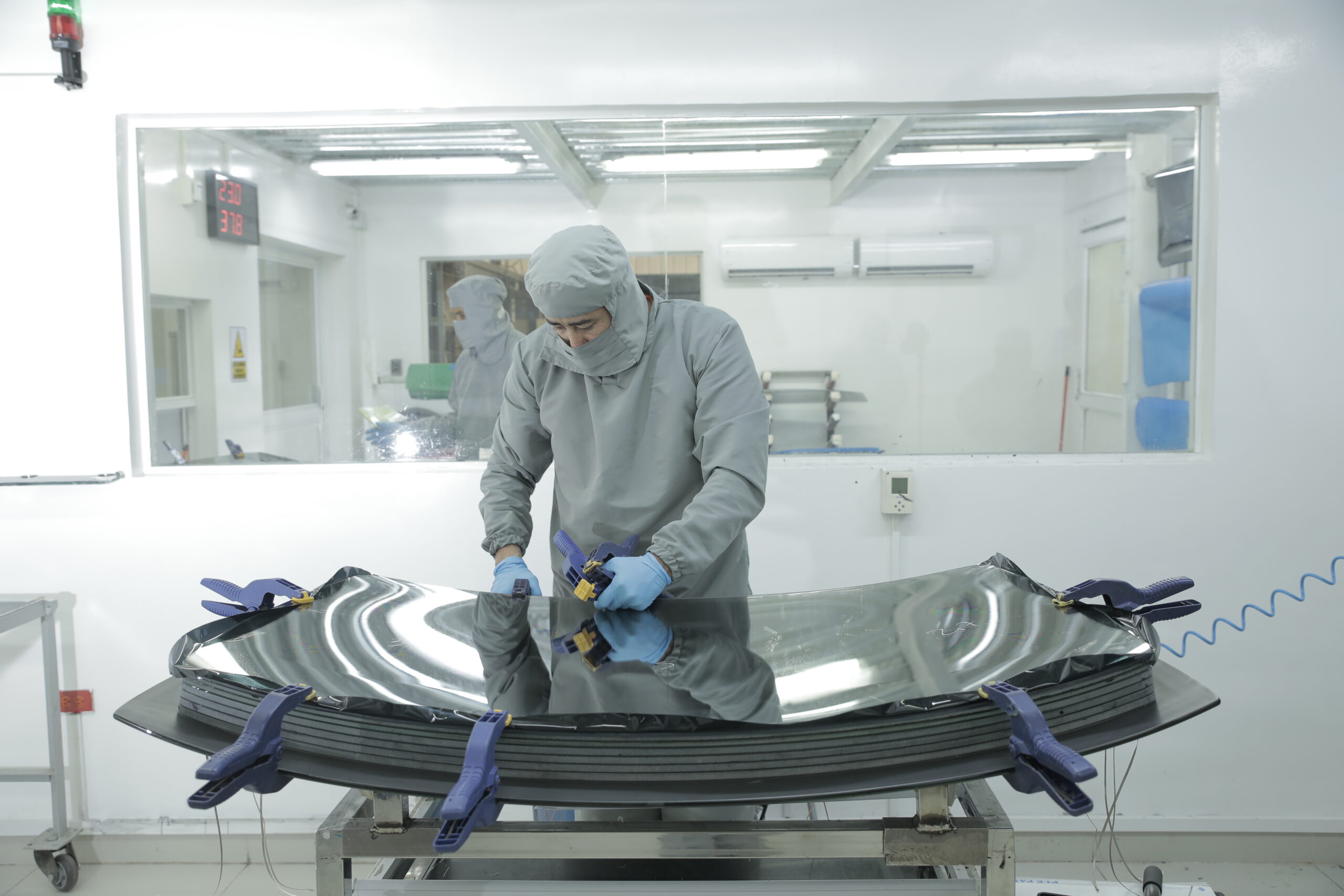
In-house Development

New Developments
Making armored glass requires a lot of metal
Our metal mechanic shop is important to Optima’s R&D strategy. We develop and elaborate our molds and steel inserts.
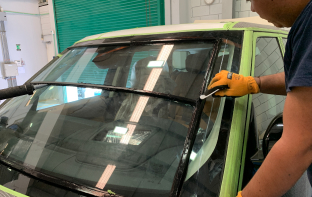
Freezing
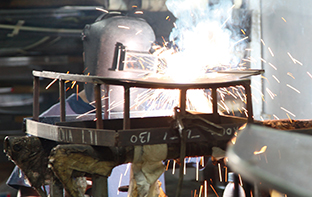
Curved Molds
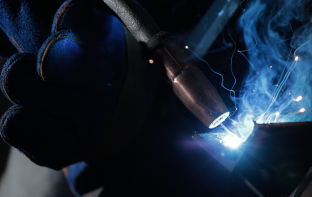
Steel
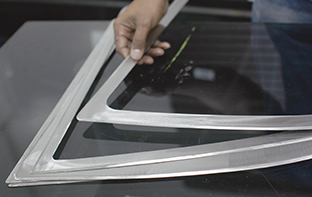
We have strict control of the steel insert chamfer
Total control of painted surfaces
Why is the painting process so important for us? The answer is: originality.
The black outline is used in armored glasses for several purposes. In the fixed parts, it serves to hide the adhesive that joins the glass to the vehicle body. In the moving parts such as side windows, it is used to hide the steel inserts.
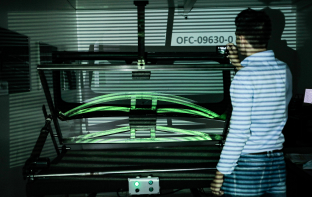
In-house design, photo mechanics and screen-printing process
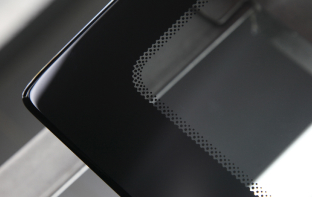
Dot Matrix
Technological Support and Production Engineering
Manufacturing is constantly evolving from production based on manual processes to computer assisted automated processes. In the armored glass industry, we have to keep learning and implementing new technologies.
At Optima we permanently invest in training our engineers and adopting new technologies that improve our products and process.
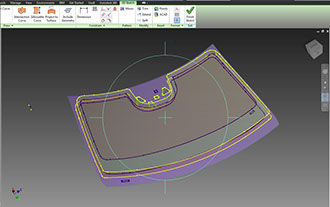
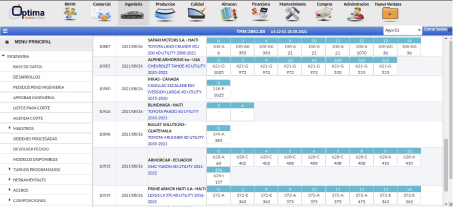
CAD Computer Aided Design
CAM Computer Aided Manufacturing
Systematizing operations
We design and produce our molds and steel inserts in-house.